ニュース
ラティス・テクノロジーから発信する情報
お知らせ
製造業の DX に 3D で貢献する|14.現地現物を DX に活かす(1)
2021年2月19日
14.現地現物を DX に活かす(1)
ラティス・テクノロジー株式会社 代表取締役社長 鳥谷 浩志
年初早々、首都圏は二度目の緊急事態の発出となりました。思い返せば、年末は新宿も渋谷も銀座も、かなりの人出でした。新型コロナの 8 割が無症状であることを思えば、街を行き交う人々の中にも相当の感染者がおり、その人々と談笑し会食することで感染が連鎖するといったことが随所で起こっていたのでしょう。新型コロナ発見グラスのようなメガネがあって、誰が感染者か即座に分かるようにならないかなどと妄想してしまいます。
現実の感染者を即座に見える化できていれば、誰もが危機感を持って、もっと迅速に行動を変え、緊急事態も避けられたかもしれません。しかし、現段階では現実を即座に把握するのは難しいでしょう。同様に、製造業における現地現物の把握、つまり、デジタル化というのは、製造現場のデジタル・トランスフォーメーション (DX) を進める上で難題です。今回は、現地現物をどうデジタル化するかについて説明しましょう。

パンデミックが変えた社会、変えられない現地現物
コロナ前には、経済産業省が Society5.0 を唱え、仮想空間と現実空間を高度に融合させたシステムにより、経済発展と社会的課題の解決を両立し、人間中心の社会を構築するとしていました。2020、21年と二回に渡る緊急事態宣言により、日本の社会でも、ようやく在宅勤務やリモートワークが一般化し、デジタルシフトが一気に進もうとしています。
そこに取り残されたのが、製造業の、特に現地現物を扱う生産技術や工場部門といった製造現場です。各種の調査データを見ても、現場の労働者は製造業の全部門の中で、突出して出勤率が高く、医療従事者のように社会的には目立ちませんが、“エッセンシャルワーカー” 化しているのです。
現地現物を 3D デジタルツイン化することができれば、製造現場の DX に活かせるでしょう。ラティスでは、自動車向けの生産設備や部品を製造する大豊精機株式会社(http://www.tsk.taihonet.co.jp/ 以下、大豊精機)をパートナーとして、点群を活用するソリューションを開発してきました。
また、同社は現地現物と 3D モデルを融合した 3D デジタルツインの業務活用で時代の最先端を行くユーザーとして、そのソリューションを実業務で利用してきました。今回は、最新の点群ソリューションと、その活用事例の実際を通して、製造現場の DX を進める方法を考えていきましょう。
現地現物を点群データ化する
近年、3D スキャンして、そのまま空間内の大量の座標値の集まり(点群)で、現物を表現してしまうという手法が普及しつつあります。3D スキャナの性能向上も著しく、最近ではカラーで点群を再現することもできます。一度スキャンしてしまえば、3D の写真として、全体像を見渡すことができますし、必要であれば任意の場所の寸法も計測できます。大豊精機が実際に 3D 計測する様子を動画でご紹介しましょう。
ご覧のように、計測器は 360 度回転して、レーザーが捉えられる形状を 3D の点の集まり、点群としてデータ化します。長距離スキャナを使えば、100 メートル先の形状もキャプチャすることができます。
しかし、一ヵ所からの計測では、影になる部分はキャプチャできないので、何カ所からか計測し、点群を 3D データとして位置合わせし、合成する必要があります。計測中に入り込んでしまった人や不要なものは、データから削除して使いやすく、かつ、見やすい点群データにする必要があります。このように点群を計測して使えるデータを作成するには相応のノウハウが必要です。
こうして計測したデータで、どんなことができるでしょうか。その例として、大豊精機の工場を点群化し、3D で再現した動画をご紹介しましょう。
このビデオでは、地球全体から大豊精機のスキャンした工場に飛ぶところまでを写真で示します。次に、工場の建屋全体を 3D の点群で表示しています。建屋を取り巻く森林や駐車場の自動車まで 3D で再現されていることが分かります。最後に、工場内の製造設備をすべて点群化したものを利用して、工場内を隈なく 3D で見せてくれます。工場設備がリアルに再現されていることが分かるでしょう。
このように点群データは現地現物をありのままに 3D 化し、その現在の姿を見える化してくれます。これだけでも、現状を把握するという意味では有効な武器になります。
点群データを入搬出シミュレーションに活用する
次に、点群データを設備の入搬出のシミュレーションにも活用する事例を紹介します。工場内の既存設備は 3D スキャンして点群データ化し、搬入する新しい生産設備は CAD で設計したものを XVL 化しておきます。
下図では、その両方を統合して表示しています。新しい設備を移動させることで、既存設備との干渉を確認することができます。重量のある設備の入搬出工事は人命にも関わる大仕事になりますから、その安全性を担保することは極めて重要です。
点群を利用した工事進捗のシミュレーションにより、リスク低減を実現することで、より安全な工事計画を立案することができます。単に見るだけでなく、デジタルデータで入搬出シミュレーションを実現できるのです。なお、下図では既存設備の点群データは機密上の理由からぼかしてあります。

データ活用の幅を格段に広げる 「点群モデル」 とは?
点群データは現地現物をビジュアルに再現する手段としては実に素晴らしいものです。しかし、3D デジタルツインとして考えたときには、致命的な問題が一つあります。
それは、スキャンされた点群は、ひとかたまりのデータとなってしまうため情報としては扱いづらく、利用範囲が限定されてしまうということです。もし、点群データが 3D CAD モデルと同等の構造を持ち、3D デジタルツインとして扱えるようになったら、その活用範囲は飛躍的に広がるはずです。
たとえば XVL 上で提供されている組立アニメーションや、特定のユニットだけを移動しながらの動的な干渉など、3D モデルを使った検証機能がすべて適用できるようになります。では、どうすれば点群データを 3D デジタルツイン化できるでしょうか?
これまで一般的だったのは、点群データを参照して 3D モデルをオペレータがモデリングする手法です。たとえば、パイプの円柱形状のような単純なものは簡単にモデル化できます。しかし、この方法では、複雑な曲面形状をモデル化するのに莫大な手間がかかってしまいます。初めから CAD で作成するのと変わらなくなってしまうのです。これでは、何のために点群測定をしたのか、その意味がなくなってしまいます。
そこで、点群データを実際の設備のユニット単位に分割し、3D CAD モデルと同じようにアセンブリ構造を定義する手法をラティスと大豊精機で共同開発しました。この方法を実際に、大豊精機が検証したところ、驚くべき結果が得られました。
床面積 400㎡ の工場の場合、現地の計測からデータ準備完了までの時間は、3D モデリングした場合と比較して 1/10 程度に短縮されました。新手法によって、圧倒的に短い時間とコストで現地現物を 3D デジタルツイン化できることが分かったのです。
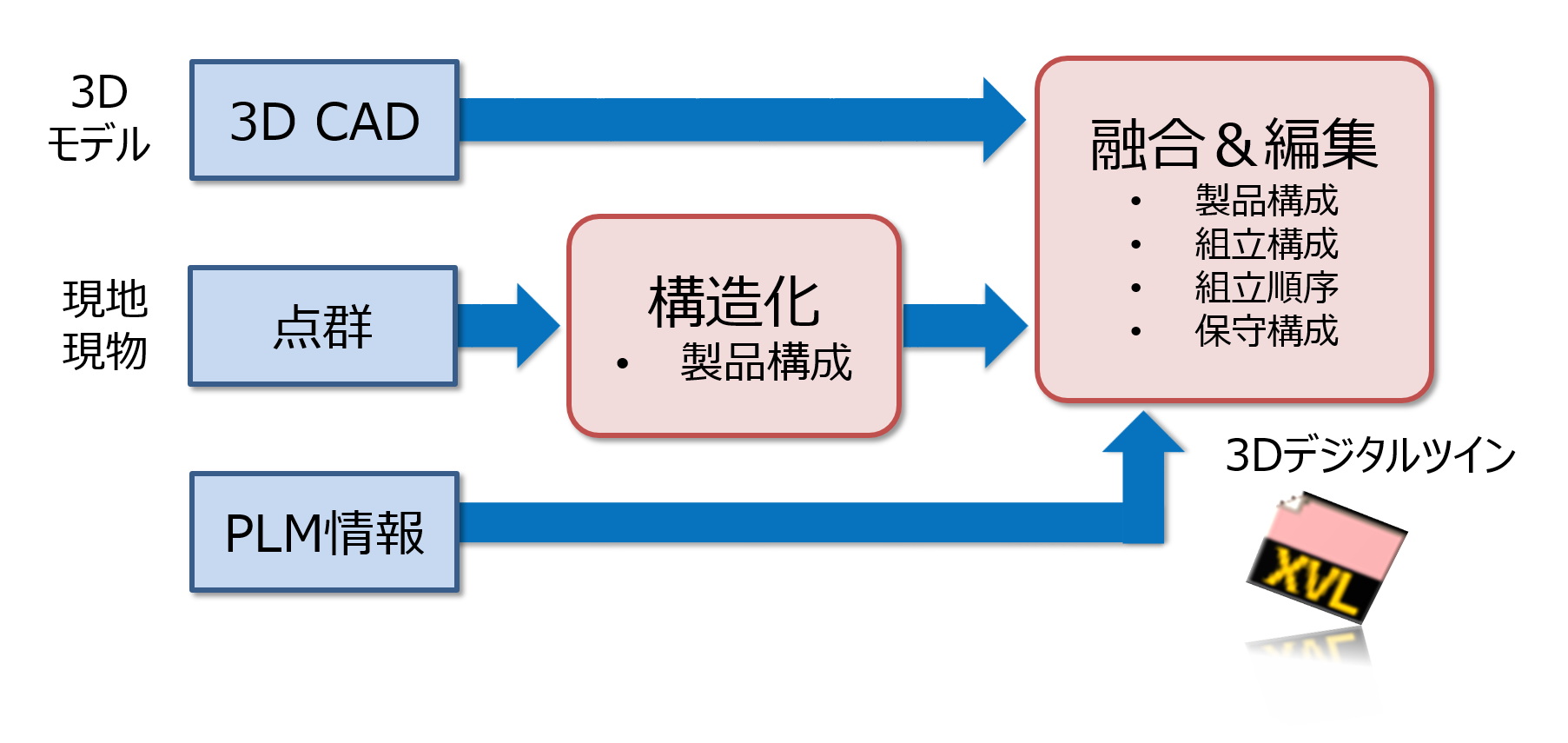
現地現物を構造化する 「点群モデル」 の実際
点群データを構造化することで 「点群モデル」 となれば、CAD データと同等に扱えるようになり、CAD モデルと融合して XVL の中で、3D デジタルツインとして扱えるようになります。「点群モデル」 を実際の例で考えてみましょう。
下図では、左の工場内の設備の点群データを、右の色分けされた構造に分け、製品のアセンブリ構造を定義しています。こうして、ひとかたまりだった点群データが、3D モデルとして扱えるようになります。一部の設備ユニットだけを移動して干渉をチェックすることで入搬出できるかを詳細に検証できるようになるのです。点群はデータ容量が大きいので、3D モデル内に統合するにはXVLのような超軽量表現を利用することが極めて有効です。

「点群モデル」 を設備の入搬出シミュレーションに活かす
では、点群モデルを利用すると入搬出シミュレーションはどう進化するのでしょうか。大豊精機で実施した設備の置き換えを例に見てみましょう。
下図の既存設備を置き換えたい場合、3D スキャンした点群データをあらかじめ、点群モデル化しておきます。これによって、設備のアセンブリ構造が定義されます。それを参照しながら、撤去する設備本体やそこにつながる付属ユニット、配線や配管を除去していくのです。こうして、設備とそれに関わる不要な設備の撤去作業をデジタルで事前検証できます。また、撤去後の状態を再現することで、新設備が入るかの確認や新設備のレイアウトを検討することができます。

このように XVL による 3D デジタルツインを活用することで、現物を利用して、現実に即した詳細な 3D シミュレーションが可能になったのです。
図面を使って、空間検証する
製造現場の DX を進める上では、工場も設備も 3D 設計されている姿が理想です。しかし、現実には、まだまだ 2D 設計が主体となっている現場が多いのが事実です。ところが、このような 3D 設計されていない工場ですら、3D を有効に使う手段があります。
点群モデルという工場の 3D デジタルツインを使うと、2D 図面で空間検証が可能になるので、これまでの設計手法を変える必要がないのです。大豊精機で実践している方法を紹介しましょう。
点群データを点群モデル化し、不要な設備を撤去しておきます。そこに最新の設備を設計した図面を投影するのです。必要な設備はそのまま残しておけば、視認するだけで、新設備と既存設備との干渉を見つけることができます。新設備設置の際の障害物を発見することができるのです。現物と図面データで空間検証することも、XVL による 3D デジタルツインにより実現することができます。

このような手法は現場で点群データさえ準備すれば、すぐトライすることができるため、製造現場の DX を実現する第一歩として、今すぐ実践できる現実的な手法です。ラティスと大豊精機はこうして、製造現場での点群活用手法のノウハウを蓄積してきました。
3D デジタルツインの有効性は、一度、自社データで体験してみないと分かりません。しかし、いきなり点群計測からモデル化、安全性や入搬出検証となると尻込みする現場も多いでしょう。そこで、待ったなしの DX にチャレンジしようという企業向けに、両社でそれを支援しようというサービスを始めています。
関心ある方は、ソリューションお問合せ窓口から 「点群サービスに興味あり」 とご連絡ください。
アフターコロナ時代の製造業に貢献する
人口 570万人のシンガポールでは、新型コロナ感染への累計の検査回数が 540万回にも達しているといいます。ここまでやれば、まさに、現実の感染者をデジタル情報として適格に把握して、対処できるでしょう。シンガポールでは、一時、外国人労働者の間で感染が広がったことがニュースになりましたが、最近では市中感染がゼロの日が多く、死亡率も他国とはけた違いに低いといいます。日本のコロナ感染把握もしっかりやって、早くこれまでの日常が取り戻せればと期待します。製造現場の DX も、現地現物の 3D デジタルツイン化によって加速できるでしょう。本コラムがその一助となればと願っています。
今回のお話はここまで。次回のコラムをお楽しみに。
・XVL はラティス・テクノロジー株式会社の登録商標です。
・その他記載されている会社名および製品名は各社の登録商標または商標です。
(関連 XVL 情報)
・点群モデルによる生産設備検証ソリューション:紹介ページ(サイト内ページにリンクします)
・点群データを点群モデル化するXVL Studio Hybrid:紹介ページ(サイト内ページにリンクします)
著者プロフィール
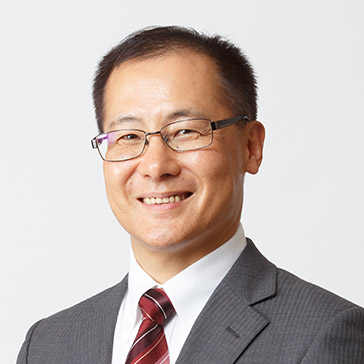
鳥谷 浩志(とりや ひろし)
ラティス・テクノロジー株式会社 代表取締役社長/理学博士。株式会社リコーで 3D の研究、事業化に携わった後、1998年にラティス・テクノロジーの代表取締役に就任。超軽量 3D 技術の 「XVL」 の開発指揮後、製造業のデジタルトランスフォーメーション(DX)を 3D で実現することに奔走する。XVL は東京都ベンチャー大賞優秀賞、日経優秀製品サービス賞など、受賞多数。内閣府研究開発型ベンチャープロジェクトチーム委員、経済産業省産業構造審議会新成長政策部会、東京都中小企業振興対策審議会委員などを歴任。著書に 「製造業の 3D テクノロジー活用戦略」 「3次元ものづくり革新」 「3D デジタル現場力」 「3D デジタルドキュメント革新」 などがある。
最新の XVL 関連情報を知りたい方へ