ニュース
ラティス・テクノロジーから発信する情報
お知らせ
SPECIAL 対談|東京大学 ものづくり経営研究センター × ラティス・テクノロジー
2023年5月9日
2023年
5月
「産学連携で製造業の未来を拓く」
知識交流と創造のプラットフォームで製造業を支える
本日は東京大学大学院経済学研究科付属経営教育研究センター (MERC:Management Education and Research Center、以下 MERC) を訪問し、センター長の新宅 純二郎 教授に、昨今の世界情勢を踏まえた日本の製造業への提言を伺いました。
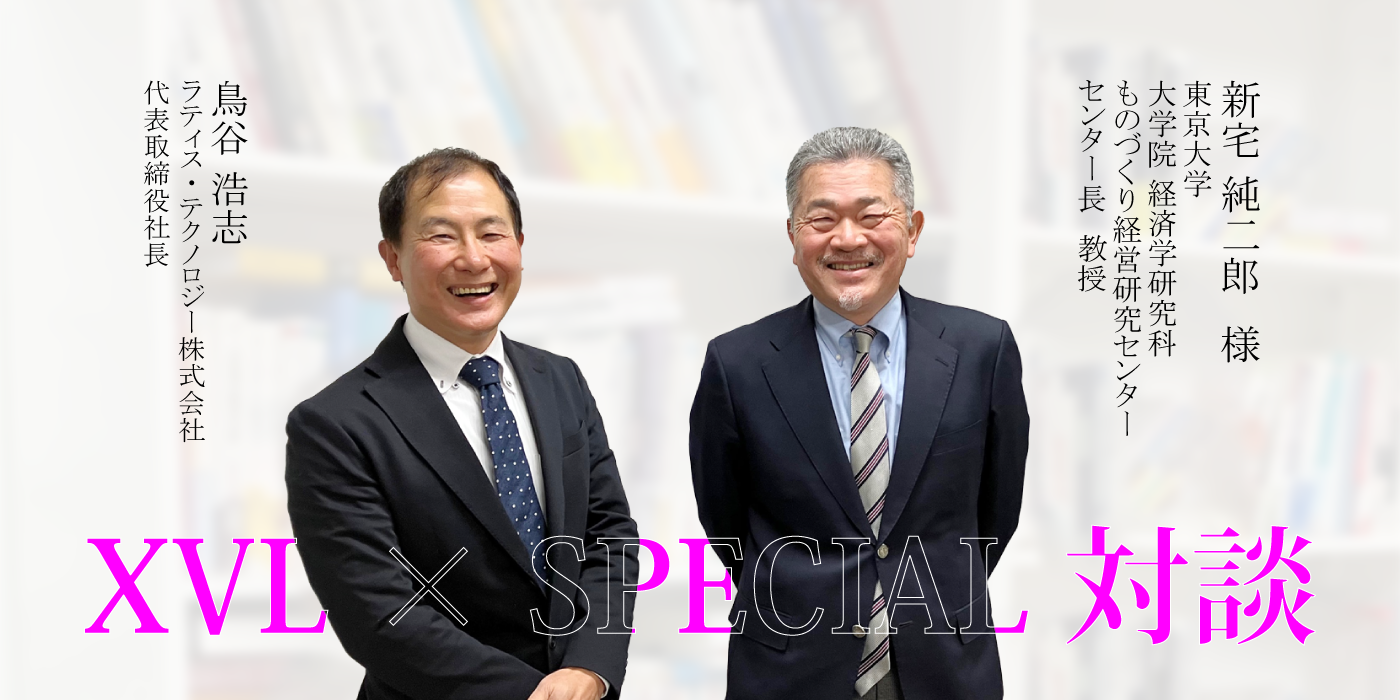
鳥谷:
2022年の年末に開催されたMERCセミナーでは、ラティスの “製造業 DX × 3D” を紹介する機会をいただき、ありがとうございました。今回は、新宅先生のお話を伺いに来ました。先生はどのような経緯で研究の道を志したのでしょうか?
新宅:
私は、東京大学の経済学部経済学科に入学、そこからいわゆる転科して経営学科へと移りました。経済学科の時には就職を意識していたのですが、経営学科で勉強していく中で、企業組織よりも学問の道の方が向いていると思うようになり、研究の道へと歩み始めました。。
鳥谷:
現在は MERC のセンター長ということですが、どういう研究をされてきたのでしょう。先生の博士論文はどのようなテーマだったのでしょうか?
新宅:
新しい技術が入ることで、産業が、どのようにこれまでと異なる成長を遂げていくのか、その姿を研究しました。研究の中では、機械式からクォーツ式へと技術転換し、大きく変貌を遂げたウオッチ産業に加え、カラーテレビ、電卓のケースを取り上げました。既存の競争概念や戦略論の通説を越えて何が起こっていたのか、日本企業が世界市場で強力な外国企業を駆逐して圧倒的なシェアを得たのは何故かを徹底分析し、『日本企業の競争戦略』 という著書にまとめて 1992年に出版しました。
鳥谷:
博士論文がそのまま書籍になって出版されたわけですね。素晴らしいですね。まさに 1980年代といえば、日本の製造業が隆盛を極めた時代の競争戦略の話ですね。この本の出版から今に至る 30年、この時代は失われた 20年とか 30年と言われるわけですが、これにはどうお考えでしょうか?
新宅:
それは物事をどのように見るかによると思います。1990年代は日本の製造業にとってダメな時代だと評されるのですが、液晶ディスプレイやフラッシュメモリ、DVD などの光ディスクといった技術が日本で開発され、商品化された時代です。欧米で商品化されていた商品の後追いだった日本の製造業が、ようやく日本生まれの技術と商品を世界に打ち出した時代だったのです。
鳥谷:
VHS ビデオから DVD、Blu-ray 初期まで日本の電機産業には勢いがまだありました。やがて液晶や半導体など事業化という観点では海外の後塵を拝するようになります。この点に関してはどのようなご意見をお持ちですか。
新宅:
確かに液晶や、半導体を作るという観点では海外勢に取って代わられた感はあります。しかしながら、より広い視点で見ると、それらを作る製造装置や素材では、アルバックや、東京エレクトロン、信越化学工業など日本企業が市場で重要なポジションにあり、海外勢もそれらの会社に依存しているという実態があります。
鳥谷:
業界全体として、日本の製造業の強みとするポジションが変わったということでしょうか。産業規模という観点では、いかがなのでしょうか?
新宅:
液晶パネル産業で具体的に説明しましょう。この産業が本格的に立ち上がった 1992年は材料、部品、パネル製造までほとんどの付加価値を日本企業が占めていましたが、その規模は 40億ドル程度でした。それが 2004年には 600億ドルに成長しました。しかし、韓国企業や台湾企業の参入で日本企業のシェアはパネルでは 50% を切りました。しかし、部材や製造装置では高いシェアを維持していました。そういった部材の付加価値まで含めて、日本企業のシェアは少なくとも半分はありました。そうすると、日本の液晶パネル関連産業は、1992年の 40億ドルから 2004年には 300億ドルに成長したということになります。
パネル製造レベルではシェアを失ったが、産業全体としては成長産業として GDP に寄与したというのが事実です。垂直的な付加価値ではシェアを失ったが、パイ全体が伸びたので、結果として成長したわけです。半導体産業などでも、同様のことが起きてきたのではないでしょうか。
鳥谷:
非常にわかりやすい説明ありがとうございます。多面的なものの見方が必要ですね。
新宅:
2000年代、日本企業が海外に続々と進出しました。現地での生産が増える一方、日本からの輸出量も大幅に増えているという事実も、一般の方が抱くイメージとは異なるのかもしれません。
鳥谷:
確かに、国内で作っていた分を海外で生産するわけですから、日本からの輸出金額は少なくなりそうなものですね。どう理解すればよいでしょうか?
新宅:
海外に進出した企業は、現地での調達率を引き上げようとします。しかし、日本から現地に送り出す部品・材料は、ある一定水準を下回ることはないというのが現状です。1次部品は現地化できても、2次、3次のレベルでは日本への依存が高いということもあります。あるメーカでは 10年以上かけて 2次、3次レベルでの現地化に取り組んだのですが、純粋な現地調達率は 7割程度に留まったと聞いています。
鳥谷:
2011年には 1ドル 75円という超円高の時代がありました。日本の本社から現地化をより進めろ、という指令が出ていたのではないかと察しますが、それでも 3割は日本からの輸出だったというわけですね。実際には何が起こっていたのでしょうか。
新宅:
海外で生産しても、基幹となる部材や中間財は日本から輸出する必要があるというからくりがあるためです。ハイブリッド車に必要な先端品や、精密な金型の製作やその調整技術などは、なかなか現地化は難しいのです。ドイツの自動車メーカの中国工場の方と話す機会があったのですが、基幹部品はやはりドイツから輸入しているとのことでした。
鳥谷:
これは、先ほどの液晶や半導体産業の変化と同じ構造ですね。
新宅:
その通りです。中国や ASEAN に工場が進出すると製品価格は下がり、製品においては日本企業の取り分は少なくなります。しかし、その中でも、原材料や基幹部品など付加価値の高い部分では日本製が利用され、日本の取り分が少なくなるかというとそうではないのです。
鳥谷:
失われた 30年と聞くと、経済的な指標がおしなべて悲観的な数字ばかりになっていると思っていました。
新宅:
楽観主義的かもしれませんが、私はそう思っています。鉄だって、長らく駄目だといわれながら、しっかりと存在感を示し続けています。造船業も然りです。また舶用部品は、日本製の信頼が厚く、海外で作られている船舶でも広く利用されています。最近では、韓国で安く船を調達し、一度目のメンテナンスの際に、ボルトなどの重要な部品を日本製に置き換えるというような動きもあると聞いています。そうすると一番コストパフォーマンスがよくなるそうです。とはいえ、競合も技術がわかってくると思うので、日本も走り続けなければ差が詰まってしまいます。
鳥谷:
ラティスも走り続ける製造業を支える 3D 技術を絶えず進化させ提供しています。ところで、センター長をされている MERC においては、どのようなことをやられているのでしょうか。
新宅:
もともとは、2002年に文部科学省 (通称:文科省) が 「21世紀 COE プログラム」 (The 21st Century Center Of Excellence Program) という、日本のいろんな研究分野の中でも勝てるところにだけ集中的に研究資金を投下しよう、という枠組みを作ったのですが、それに応募するべく前任の藤本 隆宏 先生 (現 早稲田大学教授) と 2003年にプロジェクトを立ち上げました。
1990年代には製造業の競争力を回復させようとして、経済産業省などで様々なプロジェクトが立ち上げられ我々も協力してきました。しかしながら、そういった政府のプロジェクトは単年度でプログラムを回しており、長期的な取り組みにつながりません。そこで大学を拠点にして、腰を据えて、ものづくり、製造業の経営問題に取り組もうと 21世紀 COE プロジェクトとして 「MMRC (ものづくり経営研究センター)」 を立ち上げました。これが現在の MERC の前身となりました。
鳥谷:
文科省の 21世紀 COE プログラムに応募することから始まったのですね。藤本先生、新宅先生とは長いお付き合いですが、存じ上げませんでした。
新宅:
現在 MERC の柱は二つあります。
一つは、2004年の春から、産学連携を進めることを狙いに、「ものづくり経営研究コンソーシアム」 を立ち上げました。藤本先生と 2人でご縁のあるところを回って、トヨタさん、キヤノンさんを始めとして業種関係なく、繋がりがあった会社さんを口説いて回って17社で立ち上げました。そこから月 1回の研究会を開催しており、現在、研究会開催は 220回となっています。
鳥谷:
そんなに回数を重ねているのですね、私も先日、研究会で久々にリアルにお話する機会をいただき、ある会社さんとビジネスの話を進めています。各社に出会いの場を提供しコラボレーションを進める、大変良い機会ですね。
新宅:
ものづくりにおいて業種を超えて率直に議論する場というのは少ないので、そこに価値を認めてくれる企業も多く、加盟社は年々増加してピーク時は 34社、現在 28社です。研究会の場以外でも、どこの会社の工場を見学に行きましたとか、協業を始めたという話はちょくちょく聞いているので、我々の知らないところでも貢献しているのではと思っております。新型コロナのせいで、この 2、3年リアルに会えない状況にはなってしまっていましたが、今後は月一回、定期的に集まる場を提供したいと考えています。
鳥谷:
オンライン化が進んで便利になった反面、やはり対面でなければ生み出せないアイデアや人と人との関係構築といった価値が確かにあります。MERC のもう一つの柱は何でしょうか?
新宅:
もう一つが、2005年に始めた 「ものづくりインストラクター養成スクール™」 です。当時、団塊の世代がどんどんリタイアする 2007年問題が言われておりました。ものづくりでは、団塊の世代は国内の工場で活躍し、また欧米やアジアの海外工場の立ち上げでも中心になった世代です。そういう世代の知見を活用できなくなるのは、企業にとっても、日本にとっても損失なので、そういった方々が活躍する場を作っていこうと立ち上げました。こちらも今では 18期、180名ほどの人材を輩出しています。
鳥谷:
日本の製造業を支えてきた技術者の知見を伝承する仕組みを構築してきたのですね。具体的にはどのようなことをされているのでしょう?
新宅:
カリキュラムを通じて、ゼロから知識・スキルを植え付けるわけではなく、既に持っている知識・スキルを汎用化させ、異なるフィールドで生かしていただくようにしております。社内用語や業界用語で語っていたことを一般的な概念で語れるようにするということです。
実際にあった例としては、コピー複合機の工場の責任者を務められていた方が参加されていました。その方は、複合機に関する知見は豊富で何でも分かる一方、その他の製品に関しては全く知見がない状態でした。しかしながら、製造ラインを滞りなく回す高度な知見を持っていました。実際、カメラを作る工場で指導を行い、力を存分に発揮されました。大半の中小企業では、ものの流れを管理・指導できる人材が欲しいのですが、なかなか支払える金額の範囲では見つけられせん。
鳥谷:
それは引退する技術者とノウハウを求める中小企業の両者にとって、まさしく Win-Win の関係ですね。
新宅:
我々がスクールを立ち上げた数年後に、地方自治体の産業振興の方から、地場の製造企業を強化するため、ものづくりインストラクター養成スクールを立ち上げたいので支援して欲しいという依頼をたくさん受けています。群馬、滋賀を筆頭に、現在 14、15か所で行われています。参加されているのは、地元の大企業をリタイアされた方や、地元の中小企業の現役というのが大半です。現役は自分の現場を改善し、リタイア組は中小企業のお手伝いというところで、人材を循環させる役割を担っています。現在は製造業の知見を、製造業内で活用することが主ですが、そういった知見をサービス産業に展開することも可能だと思っています。
鳥谷:
それは非常に面白いお話で、可能性を感じます。ところで昨今、VUCA(Volatility:変動性、Uncertainty:不確実性、Complexity:複雑性、Ambiguity:曖昧性) と言う言葉に象徴されるように、変化の激しい時代と言われておりますが、それはどのように製造業に影響を与えているのでしょうか。
新宅:
2000年代グローバル化が一気に進みました。2010年代には、ロシアのクリミア併合があり、シリア、リビア、アフガン、アルメニアなどで紛争が起こりました。そしてここ数年、アメリカと中国の対立が激化しています。既に 2012年ごろには、ファーウェイを締め出そうという動きがアメリカであったと聞いており、アメリカは当時から現在の状態をある程度予見していたのだと思います。米中対立がこれまでの対立と異なる点は、経済の衝突を起点にして、国家間の関係性が悪化している点にあります。しかしながら、如何に関係が悪化しても、米中をつなぐ経済の線を断ち切ることはできず、後戻りはできません。
鳥谷:
一方で、サプライチェーンのグローバル化がもたらす問題もあります。コロナ禍やウクライナ紛争により半導体や部材の調達が難しくなり、自動車の生産などが滞っていると聞きます。
新宅:
グローバル化が進むと、部材を安く調達するために、アジアやヨーロッパなどからの輸入も増えます。輸入となると、輸送のリードタイムなども考慮しなければならず、部品在庫をほとんど持たないことのリスクは高まります。先般、給湯器が半年、1年待ちという状況になっているという問題があり、経産省の担当者が調査したところ、ワイヤーハーネスをベトナムから調達できなくなっていることに起因していることがわかりました。しかし、さらに調査をしてみると、ベトナムでの生産が滞っていた理由は、ベトナム工場がワイヤーハーネスの部材を日本から調達しており、その日本工場がボトルネックになっているためでした。
鳥谷:
根本の原因は日本だったわけですね。サプライチェーンが非常に入り組んで複雑化していることが分かります。
新宅:
日本の製造業において長年 QCD (Quality:品質、Cost:価格、Delivery:流通) が重要視されてきました。その中でも昨今コストへフォーカスが偏り過ぎた結果、サプライチェーンがグローバル化、複雑化してその結果、流通に支障をきたし、販売機会をロスしてしまうことが多いのです。欲しいものを、欲しいタイミングで届けられないと高い価格で売れません。コストを下げようした結果、利益を損なってしまうことは大きな問題です。
鳥谷:
まさに経営の問題ですね。昨今では、DX (デジタルトランスフォーメーション) がメディアを賑わせていますが、新宅先生はどのように捉えられていますか。
新宅:
メディアが作り出した典型的なバズワードですね。
重要なのは、デジタルで各社がどのように変わっていくかです。日本では擦り合わせ型のものづくりに強みがあります。とはいえ、開発と製造には見えない壁があり、改善する余地が大いに残っていると思います。デジタル化を進めて部門の仕事が改善されたという話は多いですが、全社での成功事例はほとんど聞いたことがありません。
ラティスさんの XVL ソリューションは、全社で活用するというコンセプトなので、部門間の風通しを良くし、全社での業務を改善する、非常に有効なツールだと思っています。
鳥谷:
ありがとうございます。ご指摘頂いたように、組立性の検討 を XVL で行い、それを設計にフィードバックするという、開発と製造のコラボレーションのソリューションとして実績は積み上がってきております。最近ではサービス部門から開発へフィードバックする事例が出てきています。
昨今では、多くの企業様がサービス領域に力を入れており、最前線でお客様からダイレクトに意見をもらったり、サービスやメンテナンスを提供する際の困りごとに直面したり、そういった情報をデジタルで開発にフィードバックする意味は大きいと思います。たとえば、VR 空間で作業性の検討を行える技術 で、開発へのフィードバックを支援しています。また、サービス現場において 作業手順をタブレットを使って 3D で確認 できる仕組みを提供しています。
新宅:
サービス部門から開発へのフィードバックも面白い話で可能性を感じますね。とはいえ、やはりデジタルはデジタルでしかなく、DX に関してはトップが引っ張るぐらいでやらなければ成功はおぼつかないと思います。DX を冠する部署を作って後はよろしくでは上手くいきません。データは繋げるからこそ価値があり、部門を越えてこそ価値があるのです。
鳥谷:
まさに我々の XVL パイプラインは 3D の設計情報というデータで部門を繋ぐというコンセプトで開発をしています。部門の利害が絡みますので、トップの出番がきます。その先のビジネスモデルの組み換えまで来るとますます難易度が上がり、トップの役割が重要になります。
新宅:
これは何も日本の企業だけに限ったことでなく SAP でも本社があるドイツでは、なかなかビジネスの組み換えを行うことができませんでした。そこでアメリカ西海岸に Design Thinking のアプローチを活用して新規事業を立ち上げる拠点を設けて、それを機に、本体の変革を実現したと聞いています。日本でも本体から切り込むことは難しいとは思うので、本体でないところで成功事例をつくり、そこをというのが良いのではと思います。
鳥谷:
日本の企業だけでなく、海外企業、SAP のような先端のイメージがある企業でも DX には苦労しているのですね。それを聞いて、少し安心しました。ところで、自動車業界においても、EV 化の進展で、擦り合わせを強みとする日本の製造業の危機が叫ばれるなど将来は不透明です。日本の製造業を元気にするメッセージをいただけませんか。
新宅:
私は、仕事柄、中小企業への視察も頻繁に行っているのですが、世間一般には知られてはいないが素晴らしい技術をもっている企業が、日本には本当にたくさんあります。こういった企業が日本の製造業を支えているわけです。
車や家電などの完成品メーカに目が行きがちですが、日本には、鉄鋼業もあれば、化学素材や、紡績もあります。私が製造業を研究する中で日々思っているのは、多岐にわたる業種の極めて広い裾野が広がっている国は、日本をおいて他にないということです。これは日本の製造業の大きな強みです。
先日視察した会社ではかつて公衆電話を作っていました。携帯電話が拡がり経営危機に直面しましたが、現在はロールスロイスのエンジンに携わっています。話を聞いてみると、何ら新しい技術を開発したわけではなく、持っていた技術を転用したとのことでした。
必ずしも新技術に捕らわれることなく、別の業界で技術の出口を見つけてやれば良いのです。日本の製造業は、素晴らしい技術をたくさん持っており、まだまだ成長の可能性があると思っています。
鳥谷:
先ほど伺ったものづくりインストラクター養成スクールにも通ずる話ですね。今日は、日本の製造業について新宅先生ならではの視点で解説をしていただき、非常に勉強になりました。最後に元気になるメッセージもいただき、大変ありがとうございました。
END
・XVL はラティス・テクノロジー株式会社の登録商標です。その他記載されている会社名および製品名は各社の登録商標または商標です。
最新の XVL 関連情報をお届けする XVL メルマガを配信しています!
その他の SPECIAL 対談記事こちらから
SPECIAL 対談|「産学連携で製造業の未来を拓く」
知識交流と創造のプラットフォームで製造業を支える