ニュース
ラティス・テクノロジーから発信する情報
お知らせ
XVL対談|株式会社シマノ × ラティス・テクノロジー
2025年6月17日
2025年
6月
製造業の3D化への道しるべ
~シマノはデジタル変革をいかに進めたか~
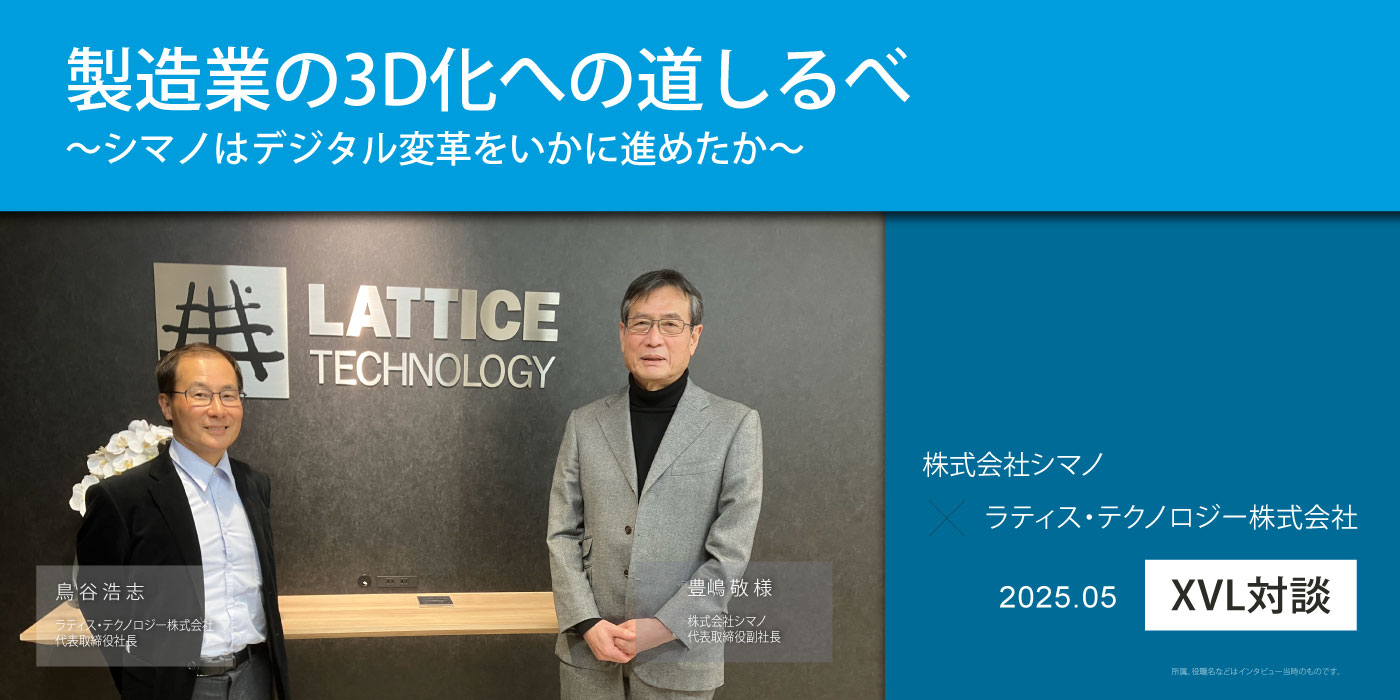
今回の対談では、設計の3D化と業務変革を強力なトップダウンで推し進め、成功に導かれた、株式会社シマノ(本社:大阪府堺市、ホームページ:https://www.shimano.com/jp/、以下:シマノ)の代表取締役副社長 豊嶋 敬 様をお招きして、その成功のポイントをお伺いします。
鳥谷:本日は、お忙しいところお時間をいただきありがとうございます。シマノの副社長、豊嶋さんをお迎えして、設計の3D化と業務変革に成功の秘訣をお話しいただきます。シマノさんの挑戦と成功は、強力なトップダウンで3D設計を進めた事例として日本でも稀有なものです。先日、『Sakai Intelligent Plant』(チームシマノのリーディングファクトリー)で、素材加工から接着まで自働化されている最先端のものづくりを見学させていただき、今日の機会を非常に楽しみにしておりました。豊嶋さんとは、2021年に上梓した拙著、『製造業のDXを3Dで実現する』(幻冬舎、Amazonで好評発売中)に賛同いただき、ご連絡をいただいたところからのご縁となりますね。
豊嶋:3Dデータを活用しての製造業のデジタル化、効率化、また3Dの形状に必要な情報を付加しての全社での活用というところなど、私が思っていることが書いてあり、まさに我が意を得たり、でした。早速、鳥谷さんの本を100冊ほど入手して、社内の核となる人たちに配布しました。
鳥谷:その節は、お買い上げ大変有難うございました(笑)。それでは、まず会社の紹介からお願いできますでしょうか。
豊嶋:株式会社シマノは、島野 庄三郎 氏が1921年『島野鐵工所』を立ち上げたところから始まりました。創業の地の堺は江戸時代から包丁と鉄砲の街として知られ、金属加工のノウハウが蓄積されていました。島野鐵工所も、2年目には、自転車のフリーホイルの生産に着手し1970年代には、釣具事業にも参入し、現在は自転車部品と釣り具を中心に事業を行っております。
鳥谷:自転車と釣り具の売り上げはどれぐらいの比率になるのでしょうか。
豊嶋:自転車が80%、釣り具が20%ぐらいですね。
鳥谷:日本と海外の生産比率はどうなっていますか。
豊嶋:これは会社の方針として50:50ぐらいにできればと考えています。非常に大雑把に言うと、付加価値が高いものは国内で、大量に作るものは海外でという棲み分けになっています。
鳥谷:日本は複雑で価値の高いものを多品種少量生産ということですね。確か、豊嶋さんは前職でエレキの技術者でしたよね。
豊嶋:はい、ご認識の通りです。私は前職ではオリンパス株式会社(以下:オリンパス)でMO(光磁気ディスク装置)とかデジタルカメラの開発に携わっていました。1990年台の後半はデジタルカメラの出現によりカメラ市場に電機メーカーが参入してカメラの市場でのプレイヤーが変わり始めたタイミングでした。我々カメラメーカーは、電機メーカーから電子部品を買っており、液晶ディスプレイもCCD等の撮像素子も最も重要なキーデバイスを全て彼らから購入するとなると製品のコストもデリバリーも全てコントロールされることになりかねないという厳しい状況でした。
鳥谷:当時、オリンパスさんはデジカメ市場で際立った存在感を示されていたと記憶しています。私もオリンパスのデジカメを持っていました。それで電機メーカーに対抗するためにどのような対策を打たれたのでしょうか。
豊嶋:私は評判の高かったレンズを電機メーカーに売り込むことで対抗したいと考えました。しかし、当時のオリンパスでは、レンズは門外不出となっており、他社に売ってはいけないものでした。勿論、競合する会社にそれを販売するというのは論外でした。
鳥谷:確かに、敵に塩を送るようにも見える戦略です。周りの理解を得るのは一筋縄ではいかなかったでしょうね。
豊嶋:一筋縄ではいきませんでした(笑)。自社のカメラ事業とは別の組織を立ち上げカメラとは別の事業として扱ってもらうということでどうにか話は通しました。その立ち上げた組織で、世界で一番薄い3倍ズームレンズを開発し、ほとんどのデジカメメーカーの製品に採用いただけたのは素晴らしい成功体験でした。
鳥谷:それは素晴らしいですね。製品とコンポーネントビジネスの両立はなかなか大変なことです。その時成功した要因はどのようなところにあったのでしょうか。
豊嶋:当時私はデジタルカメラ部門の開発、購買部門の部長を兼務しており、後に製造及びレンズの外販事業の責任者も兼務させていただきました。製品開発とコンポーネントビジネスの両方を兼務することで、一気通貫で物事を見ることができ、指揮系統も統合され、スピード感を持って事業を推進する事ができたのが良かったのだと思っています。
鳥谷:DX(デジタルトランスフォーメーション)の本質は情報の一気通貫とそれを利用したプロセス変革です。今でいうDXを実現できる責任と権限を握ったということですね。そのような大成功をされた豊嶋さんはどのようなきっかけでシマノに入社されたのでしょう。
豊嶋:エレクトロニクス技術を使って市場に新しい付加価値を提供したいということで、会長(当時、社長)に声をかけていただき2007年シマノに入社しました。当時3年程度で結果を出そうと意気込んでいたのですが、会長からは、前職とは業界も違うし、自転車のことも知らないだろうし、3年で結果を出すのは難しいだろうと言われました。こういうことをやりましょうという構想を描き提案もしたのですが、それより先ず世界中の市場と工場を見て勉強して欲しいと言われました。
鳥谷:それはまた、大きな視座をもたれた会長ですね。まずは、現地現物を見てこいというわけですね。
豊嶋:5月に入社して、8か月もの間、技術顧問の肩書で国内外の市場、工場等々いろいろなものを見せていただきました。勿論その間に新しい業務をどう進めていくかのシナリオを作り、決裁をもらい、2008年1月から新しい組織を立上げました。
鳥谷:どのようなことから始められたのですか。
豊嶋:長年量産を実現できていなかった自転車部品の電動化に取り組みました。それまでメカトロニクス製品をほとんど生産したことのない組み立てラインだったので苦難の連続でしたが、前職時代の取引先にも協力を仰ぎ、どうにか量産まで漕ぎ付けました。それが最初のエレクトロニクスを融合した主力製品の『DURA-ACE』になります。それと並行して、全く新しいシステムにも取り組んでおり、そちらも2012年に発売開始し、市場で確固たる地位を築き、シマノとして全く新しいジャンルであるメカトロニクス製品の柱へと成長しました。
鳥谷:性能や高品質の実現には、エレキとメカの擦り合わせも必要だと思いますが、両方を見ていたのでしょうか。
豊嶋:勿論メカトロニクス製品ではメカもエレキも見ていましたが、2016年からはそれ以前からあったメカ製品の設計も見るようになりました。私はそれまで旧メカの設計部門には携わっていなかったので、1年ぐらいは様子を見ていましたが、その後メカ設計部門とメカトロニクス設計部門をシャッフルして、技術を開発する部門と、製品を設計する部門に分けました。
鳥谷:それはどのような狙いがあったのでしょうか。
豊嶋:それまでは、設計部隊が要素開発も含めてまとめてやっていましたが、それではタイトなスケジュールが要求される製品開発には間に合いません。それが現在も開発部門のベースとなっています。
鳥谷:さらっとお話しいただきましたが大きな改革ですよね。このあたりは会長の信認がなければ実現できなかったのではないでしょうか。
豊嶋:信認を得たのかどうかよくわかりません。ただ開発全体を見て欲しいと依頼され、技術開発と製品開発を分ける必要があると説明し承認を得る事ができました(笑)。それ以上何も言われていません。
鳥谷:自転車部品の電動化を成し遂げたことで信認を得て、それが3D変革をトップダウンで進める原動力となったのでしょう。
豊嶋:電動化は会長の発案でしたが、長年実現できていなかったようです。電気の土俵で勝負すると、電機メーカーが参入してきて、自分たちの首を絞めることになると考えている人も多かったからではないでしょうか。
鳥谷:会長は何故電動化に着目したのでしょうか。
豊嶋:それまでのやり方の延長線上では市場への新たな付加価値提案には限界があると感じていたのではないでしょうか。シマノの主力である自転車事業を拡大していこうとした際に、メカでやれることについてはやり切った感があり、それに加えてやはり業界を引っ張っていくのは自分たちだと、業界トップとしての矜持もあったのではと思います。
鳥谷:メカ中心で成功したので、会社全体としてはいわゆるイノベーションのジレンマになっていたのでしょうか。そこに危機感を覚えた会長は、電動化というイノベーションに挑戦しようと考えたのでしょう。技術の深化はメカで、その進化は電動化でとなれば、見事に会社の両輪になります。そこで、そのイノベーションを豊嶋さんに託したのでしょう。
豊嶋:電動化に向けて何を如何すればよいかわからないが、そういうことも含めて考えてくれる人材を探していると仰ってましたね。
鳥谷:なるほど。ところで2016年から2017年頃には、Industry4.0にも興味を持たれていたようですね。シマノ版Industry4.0ともいうべき変革に取り組まれたとも伺っております。そちらの取り組みについてもお話を聞かせて頂けますか。
豊嶋:ドイツのハノーバーで開催された製造技術の展示会への視察を会長にお勧めしたところ、その影響を強く受け、帰国後にIndustry4.0をやりたいと言いました。Industry4.0はドイツの国策なわけで当然同じことはできない。そこで作ったのが、『Shimano Digital Manufacturing』 (以下:SDM)という言葉でした。こちらはシマノ版のIndustry4.0になります。柱となっているのが業務改革と技術革新の二本柱です。
鳥谷:二本柱は具体的にはどのような内容だったのでしょうか。
豊嶋:業務改革では、形骸化したISO9001の古いプロセスを刷新し、仕事の進め方そのものを変えました。一方、技術革新では、部品の金型の設計・製造技術を刷新し、製造までの一連のプロセスを自社内で行えるように取り組みました。これらに取り組む上で大切なのは、なぜこれに取り組む必要があるのかを明確にすることです。SDMでは、まず以下の目的を掲げました。
- ✓ 新しい付加価値を(お客様に喜んでいただける機能・性能を)
✓ タイムリーに(お客様の要求する時に)
✓ 適正な価格で(価値相応な価格で)
提供する。
鳥谷:目指す目的を明示することはプロジェクト成功のキーポイントですよね。ここでようやく設計の3D化の登場でしょうか。
豊嶋:このSDMを推進していく上で、重要だったのが3Dデータの活用でした。それまでのアナログなものづくりをデジタルに変える。デジタルの3D情報を活用して、ものづくりの効率、精度、品質を上げることに挑戦したわけです。
鳥谷:まさしく3Dを活用した製造業の変革ですね。具体的にはどう進めたのでしょうか。
豊嶋:2020年6月、成型技術部という金型の設計・製造専門の組織をたちあげました。それまで難しい部品の金型は外部に委託していたのを、内部で設計・製造できる様にする為に金型の設計・製造力を強化することを目的としたプロジェクトを立ち上げましたが、プロジェクトだとなかなか思ったように動きません。
鳥谷:変革のプロセスではよく起こることです。どう対処したのでしょうか。
豊嶋:それで2020年12月から3Dデータ活用プロジェクトというものを立上げました。まずは製品設計部門、即ち上流工程の開発・設計者が3D CADを使えるようにしなければならない。その年の頭からメカの開発・設計者全員に向けた3D設計の教育を始めました。やりたいのは3D活用ではなく、3DA(注釈付きの3次元モデル)活用です。
鳥谷:その二つの違いはどう理解すればよいでしょうか。
豊嶋:3Dでも形状だけだと使える範囲が限定されてしまい意味がありません。下流で利用できるような図面上の情報・データが加わっていてこそ意味を持ちます。私が問題だと思うのは、各部門がそれぞれ似たようなデータを入力し、管理し、使用している状況です。同じデータを社内で共有し、利用できるようにすべきでしょう。そのためには、設計の意図の入った3Dモデルである3DAであることが重要です。さらに成功に向けて、全プロセスの入口から出口までの3D化を徹底させました。
鳥谷:下流で使える情報を持たせた3Dを社内で流通させるというのは、私たちの提唱しているXVLパイプラインの考え方そのものです。その実現にはまず3Dデータが必要になります。多忙な設計者は今までの方法でも良かったのに、なぜ、3D教育?と抵抗したのではないでしょうか。具体的にどうされたのでしょう。
豊嶋:教育のプログラムを組み、2021年1月からメカの設計全員、順番に仕事を休ませて、1か月半の教育を受講させるようにしました(実際には仕事もしつつ苦労したメンバーも多くいたと聞いていますが…)。教育が終わった2023年1月から2次元の図面は廃止して、出図する図面は3次元しか受け付けないようにして退路を断ちました。
鳥谷:1か月半、設計の仕事をさせないというのはトップダウンでしかできない思い切った施策ですね。後から入って来たキャリア採用の方々はどうしているのでしょう。
豊嶋:キャリア採用で入ってきた方にも1か月半の教育を実施して、ある程度基礎を等しく理解いただいた上で業務に当たっていただくようにしています
鳥谷:図面を受け取るサプライヤー様はどういう反応だったのでしょうか。図面ベースの仕事に慣れたサプライヤー様は混乱したのではないでしょうか。
豊嶋:苦労しているサプライヤー様が多いのは事実です。しかし、中には、新しい3D図面の流通というやり方に対して積極的に取り組みたい、或いはこれまでのやり方を変えたいというサプライヤー様もあり、相談を受けた際には、先進的なサプライヤー様をご紹介したりしております。
鳥谷:3D図面に苦労しているサプライヤー様には、どのように対応しているのでしょうか。サプライヤー様の選別といったことがおきませんか。
豊嶋:対応するために時間をしっかりかける必要はあるでしょう。期限を定めて2D図面も出しますが、変革を進めるためには、あまりやりすぎてもいけない。いずれ、もう2D図面はありませんからという話になります。当然3D図面を活用した方がリードタイムは短くなるわけで、そうすれば自ずとリードタイムが短いサプライヤー様を選択することになるでしょう。
鳥谷:では次に、金型技術の内製化のトピックに移りましょう。かつて隆盛を極めた日本の金型産業は海外の企業に買収されたりして、その地位が脅かされているようにも感じます。今なぜ内製化なのでしょうか。
豊嶋:私は技術革新の肝は金型にあると考えました。しかし良い金型が出来ても、必ずしも良い製品ができるわけではありません。実際、金型の精度を上げても、モノを作ったら精度が出ないということもあります。そこで、自社の製品に必要な部品はすべて自社でできる様にするという方針を打ち出しました。結局、金型とそれを使用する製造の両方が必要で、その両方を知らなければと良いものはできません。
我々自身で金型を手掛けることで初めて金型、部品、組立のすべてを知ることができるようになりました。結果として、今では、樹脂、プレス、鍛造、表面処理、接着まですべて自社でやれるようになりつつあります。すべてを知ることで真のあるべき姿を、そして実現できる将来が見通せる様になってきています。
鳥谷:なるほど金型を手の内化し、型とそこから産み出される部品の組み合わせでベストなモノづくりを目指すということですね。それでは、3Dの形状を利用したシミュレーション、CAEの取り組みはどのような状況でしょうか。
豊嶋:CAEにも真剣に取り組んでいます。目指しているのは、設計者がCADで設計し、それを製造に渡したら仕事が終わるようにしたい。今は試作をしていますが、それをCAEで置き換えたいと考えています。
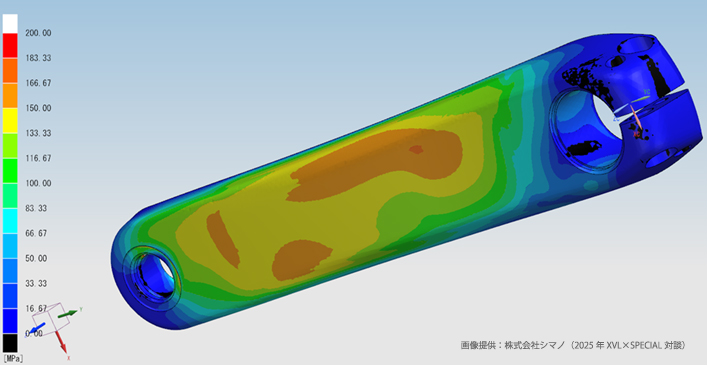
鳥谷:シマノさんの部品を組み込んだ百万円を超えるような自転車に利用される部品となると、厳しい精度や耐久性が求められるでしょう。試作で評価するプロセスをなくすのは難しいのではないでしょうか。
豊嶋:実はこれまでは、あれこれ試作して、削って、評価するという作業を繰り返していました。しかし、試作品では全ての性能の検証はできないのです。前職で半導体設計をしていた時に経験したのですが、試作を作りそれを動かすまでに半年から一年をかけていました。
しかし、そこで検証できるのは機能だけです。本来必要とするスピード(周波数)で回路を動作させる事ができないので本来の性能の検証はできません。そのためここで試作基板の作成、検証にかかる半年から一年という無駄を省く為にシミュレーションでそれを代替しました。今回のSDMでは、3Dモデルを活用してシミュレーションを実施するようにしています。最終的には試作レスで製品立ち上げをすることをミッションとしてやらせています。
鳥谷:試作レスは理想ですが、本当にデジタルだけでできるのでしょうか。効果の方はいかがですか。
豊嶋:2017年から取り組んできているのですが、この数年で格段にレベルが向上しました。以前は、難しいシミュレーションをするために非常に多くの時間がかかっていました。最近ではそれまで多くの時間を要していたシミュレーションも比較的早く終わるようになり、2024年には試作せずに立ち上がるモデルも出てきています。CAEを導入した当初は、試作して、削って、評価してという文化で育ったベテラン設計者は特に非常に懐疑的でした。しかし、取り組む中で、実機では目に見えない裏側の部分まで確認できることを知り、効果が体感できるようになると、本気でCAEに取り組むようになりました。
鳥谷:それは素晴らしい。人は変わることができるのですね!高速にシミュレーションできれば、結果を見て条件を変えて、またシミュレーションして、を高速に繰り返し精度を上げていくことができます。話を伺って感じるのは、成功の秘訣は、大きな構想を描きながら、実行の段階で、状況を見ながら打ち手を修正しながら、進められたということですね。
豊嶋:ここをこうしたら、こう動くだろうと考えても思った通りいかないことの方が多く、別の打ち手を繰り出したり、変更したり。俯瞰してみないと、それぞれの意味が分からず、この人は何をやっているのだろうと思われているかもしれません(笑)。
鳥谷:製造業においてDXの成功事例を聞くことが乏しいのは、変革をやり遂げる人材がいないところに本質的問題があると感じます。まさに、それをやり遂げてきた豊嶋さんの凄みの一端を伺うことができ、非常に刺激を受けました。最後に豊嶋さんの仕事のポリシーをお聞かせ下さい。
豊嶋:私が心がけているのは三つで、一つ目は、最後までやり切る。二つ目は、やり切ったところから始まる。その後継続できていることが重要。そして三つ目は、「日々新たなり」でチャレンジし続けること。今日の技術は、明日は陳腐化します。今日終わったことを否定する勇気が必要だということです。我々の3Dを活用しての変革を進めている中で、ラティスさんの技術や、XVLパイプラインの考え方は大いに活用できると思っています。今後とも色々ご提案いただければ嬉しいですね。
鳥谷:シマノさんの変革のお役に少しでも立てるのであれば光栄です。今後とも引き続きよろしくお願い致します。
END
【その他】
- ・XVLはラティス・テクノロジー株式会社の登録商標です。その他記載されている会社名、製品名など名称は各社の登録商標または商標です。
皆様からの感想・ご意見・ご質問を受け付けております!
最新のXVL関連情報をお届けするXVLメルマガを配信しています!
その他のSPECIAL対談記事こちらから
SPECIAL対談|製造業の3D化への道しるべ
~シマノはデジタル変革をいかに進めたか~