ニュース
ラティス・テクノロジーから発信する情報
お知らせ
製造業DX×3D成功のヒント|12.失われた30年を超えて実現する製造業DX×3D
2023年6月28日
12.失われた30年を超えて実現する製造業DX×3D
ラティス・テクノロジー株式会社 代表取締役社長 鳥谷 浩志
ウクライナからゼレンスキー大統領も駆け付けた2023年5月19日からのG7広島サミットは、被爆地での開催ということもあって印象的でした。インドなど新興国からなるグローバルサウスから代表を招き、日米欧の主要国からなるG7と、中国・ロシア陣営との綱引きも激しくなるばかりです。この三陣営の世界経済における現在のGDP比率を調べてみるとG7が4割、中国・ロシアが2割、グローバルサウスが4割です。人口動態を見れば、今後は実利を重視するグローバルサウスの比率が高まり、世界情勢はますます混沌としてきそうです。
このような中、米国は半導体などハイテク分野での中国との分断を強力に進めていますが、サミットの首脳宣言では、デカップリング(分断)ではなく、デリスキリング(リスク低減)という言葉が採択されました。つまり、大きな経済力を持つ中国を無視することはできないが、過度な依存を避けようということでしょう。日本は自由や民主主義を大事にするG7の一員でもあり、また、距離的な近さもあって中国は輸出入ともNo.1の貿易相手国になっています。中国が虎視眈々と狙う台湾もすぐ隣にあって、難しい舵取りを迫られそうです。繰り返される自然災害、減りゆく人口、伸び悩む経済力で低下する世界への影響力と日本を取り巻く環境は厳しくなるばかりです。私達にできることと言えば、個人も企業も、何があっても生き残れる準備をしておくことでしょうか。
この30年の間に製造業は何が起こっていたのか?
話を日本の製造業に的を絞っていきましょう。1990年以降、失われた 30年とも揶揄される日本において、製造業にはいったい何が起こっていたのでしょうか。伸び悩む日本経済とともに地盤沈下が進んでいたのでしょうか。先日、東京大学大学院経済学研究科付属経営教育研究センター(MERC)センター長である 新宅 純二郎 教授と対談する機会に恵まれ、この疑問をぶつけてみました。新宅教授は、1990年代こそ、それまで欧米追従であった日本の製造業が、液晶ディスプレイやDVDなど、日本生まれの技術をようやく世界に打ち出した時期であると指摘します。液晶パネルや半導体では、その後、韓国や中国メーカーとの競合で厳しい価格競争となり、日本は低迷したかに見えましたが、産業規模が桁違いに成長する中、日本企業は部品や材料といった付加価値の高い分野にシフトし、パネル関連産業というくくりでは大きな成長を遂げたといいます(図1参照)。
実際、パネル関連産業は1992年の40億ドルから2004年には300億ドルに成長し、日本のGDP拡大に貢献していたのです。しかし、思い起こしてみると、震災後の2011年には1ドル75円という超円高の時代がありました。新宅教授に製造拠点の海外移転が進み国内の製造業は空洞化してきたのではないかと問うてみると、ハイブリッド車に必要な先端品や精密な金型など、基幹となる部材や中間財は日本からの輸出が中心となっており、日本がその製造拠点であり続けたと喝破します。実際にアジアの生産拠点を訪れて、調査してみると、日本から見えているのとは、異なる風景が見えてくるのです(新宅先生との対談詳細は こちら をご参照ください)。
実は善戦していた日本の製造業
MERC を新宅教授と共同で立ち上げた早稲田大学 藤本 隆宏 教授からは、日本の製造業の輸出の実態について、次の表をいただきました。「工業製品貿易収支の推移」 と題したこの表を見ると、2008年のリーマンショックから2011年の東日本大震災に続く時期と 2020年のパンデミックの時期には低迷しましたが、それ以外は、輸出金額は一貫して成長しています。2022年には、パンデミック期の反動か円安の影響か、輸出金額は大きく伸びて史上最高の90兆円を超え 30兆円近い貿易黒字を生み、円安と原料高で悪化した日本の経常収支を下支えしています。藤本教授によれば、日本の製造業就労者数は1990年からの30年で1500万人から1100万人弱まで減少しているといいます。少し計算してみると、製造業の付加価値生産性はこの30年で約2倍に向上していることが分かります。つまり、日本の製造業は失われた30年の中でも善戦してきたといえるでしょう。
製造業の経営上の課題は何か?
では、製造業の経営上の課題は何かと新宅教授に問えば、販売機会のロスと、デジタル化に各社がどう取り組むかだと指摘します。まず、販売機会のロスに関しては、グローバル化が進展する中で、製造業はQ(Quality:品質)、C(Cost:コスト)、D(Delivery:納期)のうち、コストを重視しすぎたのではないかといいます。結果的に、サプライチェーンがグローバルに複雑化し、災害や戦乱により部材調達に支障をきたすと、製品をつくれず販売機会を失ってしまうのです。次に、デジタル化に関しては、部門の仕事が改善されたという事例はあっても、部門を超えて全社的に最適化された事例はほとんど聞きません。日本はせっかく擦り合わせ型ものづくりに強みを持つのに、開発と製造の部門間には見えない壁があって、現実には改善する余地が大きいというのです。
確かに、日本の製造業では、その強みとされる現地現物を主体とした擦り合わせや複雑な紙図面をも読み解く現場力があまりに成功しすぎて、現物や紙主体の情報流通が「部門間の風通し」を悪くしているのは否めないでしょう。実際、経済産業省の発行する 2020年のものづくり白書 を見ると、製造業の83%が後工程では、図面をベースとした仕事をしていることが分かります。多くの企業で3D設計をしているにも関わらず、紙図面や紙帳票が後工程に流れているという実態は、図面や帳票の作成の手間やアナログな情報伝達手段という点から考えても、情報流通の速度の遅さを物語っています。
DX(デジタルトランスフォーメーション)の本質は、異なる部門間で情報を迅速に共有することで、プロセスやビジネスモデルを変革することです。とすれば、製品の起点となる設計の3Dモデルと部品表(BOM:Bills of Material) 情報が統合され、それが設計部門から企業内を流通すれば、変革の大きな原動力となるでしょう。この3D情報は、製品そのものをデジタル表現する 3Dデジタルツイン ® と呼べるものです。つまり、ものづくりの源流とも呼べる設計情報を表現する図面を代替し、試作機のような実機すら置き換え可能なものになります。
こうした3Dデジタルツインを活用することで、高い生産性を実現できます。たとえば、生産技術部門では3Dデジタルツインで組立て上の問題が起こらないかを検証し、実機で起こる問題を事前につぶすことができます。その結果を3Dアニメーション付きの作業指示書として提供すれば、海外工場の立ち上げも迅速です。平時のみならず、災害や戦乱のような有事がきても、この手法は生産を継続可能にする有効な手段となるでしょう。製造ノウハウを蓄積した3D作業指示書があれば、別の製造拠点を即座に立ち上げることができます。ネットワークさえ健在であれば、VR(virtual reality:仮想現実)やAR(Augmented Reality:拡張現実)でよりリアルに情報を伝えることも可能です。こういった取り組みが原動力となって、製造業のDXが進んでいくのではないでしょうか。設計の3Dデジタルツイン情報を共有することで、組織を超えてそのデータを活用することが可能になり、「部門間の風通し」を良くすることができます。
日本の製造業のDXが成功しない3つの理由
メリットの多いDXですが、実際、日本の製造業でDXに華々しく成功したという事例はあまり聞きません。その理由はどこにあるのでしょう?ここで日本のGDPに注目してみると、2002年と2022年では550兆円前後でほとんど成長していません。この間、米国のGDPは10.9兆ドルから25.4兆ドルに右肩上がりで2.5倍増です。一方、総務省の資料 (参照先:平成30年版情報通信白書-第1章世界と日本のICT-第3節日米のICT投資の現状) を見ると、日本のICT投資は横ばい、米国のそれは右肩上がりです。ICT投資の差が、経済成長に大きな差をもたらしているのでしょうか。
ここでは、① 日本の経営環境、② 経営トップの理解不足、③ 成功体験の副作用 という3つの問題から考えてみましょう。経営環境とは日本では従業員の解雇が難しいという問題です。そもそもデジタル技術は自動化や省力化で効率を上げることが得意であり、その結果、余剰人員が生まれます。余剰人員をすぐにレイオフできる米国では、それがそのまま収益改善や株価上昇につながるので、経営陣は率先してDXに取り組むことができます。一方、解雇の難しい日本では、自動化で生み出された工数はそのまま温存され、収益の向上につながりません。収益化までは、余剰となった社員に別のスキルを身に着けてもらい、別の仕事に配置するという時間とコストが必要です。
第二は経営トップのDX化への理解が不足したまま、DX推進部のような組織を作り、そこにDXを丸投げするようなケースが多いという事実です。そこに現状維持への同調圧力という第三の要因が生まれたときDXは中途半端な形で終わります。典型的なケースを考えてみましょう。DX推進部はデジタルツールの導入を進める権限は持つが、肝心のプロセス変革まで切り込むのは困難です。これまでの方法でそれなりに成功した現場には、現状を変えたくないという消極的なしかし強い思いがあります。その圧力に負けると、DX推進部は組織やプロセスを変えずにデジタル化だけを進めてしまいます。よく考えてみると、これは古い組織やプロセスをそのまま定着させることになりますから、結果的に非生産性を拡大し、ムダなIT投資を増やすことになります。
分かりやすい例として思い浮かぶのがセブンイレブンの多彩な決済方法です。実際買い物時には極めて便利で、現金、Quoカード、商品券、nanacoやSuicaなどの電子マネー、PayPayなどのバーコード決済、クレジットカード、デビットカードなどありとあらゆる決済方法が利用できます。これは過去の決済方法をすべて継承する手法であり、消費者にとっては最高のおもてなしとなっているのは事実です。しかし、DXの視点でみれば、たとえば店頭決済をnanacoに統一すれば、IT投資も現場の負担も激減するはずです。もし、これと同じようなことを社内でもやっていたら、大変なムダではないでしょうか。旧来のプロセスをデジタル化することをDX推進部が行っていれば、こういった問題は社内随所で起こっているでしょう。DXの本質は業務プロセスや組織の改革であり、その推進はトップに委ねられるべきものです。
成功体験が生み出すデジタル家内制手工業の罠
クレイトン・クリステンセンが 「イノベーションのジレンマ」 で指摘したように、過去の成功体験が大きければ大きいほど、ビジネスの変革が難しくなります。ある事業が成功すればするほど、それを成し遂げた組織やプロセスは、その成功を実現するための形に最適化されていくからです。そこには、成功を築き上げた先輩社員がおり、カイゼンにカイゼンを重ねてきた業務プロセスがあり、リスクのある変革に立ち向かうにはあまりにも障壁が高くなります。つまり、実績を上げれば上げるほど、プロセス変革は困難になるのです。このように成功した旧プロセスを温存したままでデジタル化を進めるのは、大きなリスクです。なぜなら、古いプロセスはデジタル化によってより強固になり、企業に後ろ向きの投資を強いることになるからです。
本コラムでは、プロセスが変わらないまま、各部署にデジタルツールが乱立し、プロセス間でデータ共有ができないまま、デジタル化が進んだ状態を 「デジタル家内制手工業」 (参考:コラム) と呼んできました。トップが明確な指針を出さないとDXという名の元に強固なデジタル家内制手工業が確立してしまうのです。成功を生み出したノウハウや経験に裏打ちされた業務プロセスの変革は困難です。日本の製造業でいえば、それは現地現物ベースの擦り合わせと複雑な紙図面と紙帳票を読み解きカイゼンを進める現場力でしょう。しかし、大きな環境変化を迎えた現在、これを変えていく必要があります。ダーウィンの言葉を借りるまでもなく、生き残るものは強いものでなく、変化に追従するものだからです。では、変革に対する抵抗に打ち勝って、デジタル家内制手工業に陥らないためにはどうすればよいでしょうか?
変革を成功に導く公式とは?
米国には変革を成功に導くための Beckhard and Harris の公式と呼ばれるものがあるといいます。これによれば、変革(C)は不満(D)、ビジョン(V)、最初の一歩(F)の積として定義され、それが現場の抵抗(R)を上回ったときに成功するという不等式になっています。変革が積として定義されているということは、DやV、Fの値がゼロであれば、変革は成功しないことを意味します。つまり、現状の問題が明確でそこに不満があり、未来に対する確固たるビジョンがあり、それを実現するための最初のステップが見えていることが必須であるということです。
C = D × V × F › R
- C:Change(変革)
- D:Dissatisfaction(現状への不満、変革の契機となる)
- V:Vision(関係者の共有するビジョン、現状より良くなり、達成可能なもの)
- F:First step(ビジョンに向かう最初の一歩。実現可能なアクションプラン)
- R:Resistance(現場の抵抗)
この公式は1960年代に提唱され、1970年代にブラッシュアップされたというので、アナログな手法による変革を対象としていたはずです。しかし、その考え方はDXの時代にも色あせていません。経営トップが確固たるビジョンを持ち、組織の課題を現場と共有し、DX推進リーダーには変革に向けた最初のステップが明確に見えていることがDX成功の肝なのです。
成功への公式を製造業に当てはめてみる
これを現代の製造業に当てはめて考えてみるとどうでしょうか?めまぐるしく変わる環境の中、ニーズを捉えた製品を早く市場に供給し高収益を実現せよという株主からのプレッシャーが会社にはかかります。経営層には、現状のプロセスやビジネスモデルのままでこれを実現できるのかという不満があるでしょう。一方、現場には、人手不足の中で高品質の生産を継続せよという経営からの要望に旧来のものづくりプロセスのままで対応できるのかという不満もあるでしょう。D(Dissatisfaction)は十分に大きな値となっています。また、各社のホームページ上で公開されているIR資料を見ると、ほとんどすべての企業にデジタルによる変革に取り組むという文言があります。経営サイドもしっかりとしたビジョンを示しているのです。今、不足しているのはF(First step)、つまり、ビジョン実現と不満解消に向かって、進むべき最初の一歩は何かを見極めることでしょう。
シンプルに考えると製造業DXは設計DXとダウンストリームDXの二つからなります。そして、ダウンストリームDXの主要なものに、生技DXや工場DX、その先のサービスDXや販売DXがあります。DXの本質とは徹底的かつ効果的なデータ活用であり、3D設計が普及した現在、この3DデータをCAD/CAM/CAEといった設計DXの世界から解き放たって、部門を超えたデータ活用することがDXの起点となります。本コラムでは、これらDXを3Dでいかに実現するのか、各社の成功事例を示すことで、最初に進むべき一手を探ってきました。また、各社の事例や技術動向からも、先の公式のファーストステップ、Fの値を最大化するための方策を示してきたつもりです。
これから立ち上がる工場DXについては3D図面の最新動向 (参考:コラム) を書きました。かつて、iPhoneで世界中の人々のライフスタイルを変えたスティーブ・ジョブスはこう言いました。
「人は形にして見せてもらうまで、何が欲しいか分からない」
新しいテクノロジーやプロセスを頭の中で考えるだけでは、現実がどう変わるのか想像することが難しいのです。しかし、失われた30年の間に、各社の成功事例から3Dを活用したDXの「すでに起こった未来」が見えてきました。変革の公式をクリアして、日本の未来を製造業とITベンダーが協同で創っていく時代が来たのです。
END
【用語解説】
- ・製造業DX×3D:「製造業DX×3D」とは、現地現物のすり合わせや図面を読み解く現場力が必要な日本の製造業(=デジタル家内制手工業)に対して、XVLパイプラインによる3Dデジタルツインのデータの流れをつくることで、製造業全体でデジタルで擦り合わせが行われ、デジタルで現場力が強化されるという、日本の製造業の強みをデジタルで引き出すという考え方。
- ・ダウンストリームDX:「ダウンストリームDX」とは、設計以降の後工程でデータの流れをつくり活用することで、後工程でのデジタルによる業務変革が実現するという考え方。ラティス・テクノロジー株式会社の提供するダウンストリームDXソリューションとして主要なものに、生技DX、工場DX、サービスDX がある。
- ・XVLパイプライン:3Dデジタルツインの情報の流れをつくり、組織の垣根を超えてその情報を徹底活用することでDXを推進する仕組みのこと。
- ・3Dデジタルツイン:「3Dデジタルツイン」とは、現物と図面の双子となる3Dモデルのこと。現地現物を軽量XVLで表現し、図面情報情報をXVLに集約することで、現物に近い3Dモデル(=3D形状+構成情報+ものづくり情報)になるという考え方。
【その他】
- ・XVL、3Dデジタルツインはラティス・テクノロジー株式会社の登録商標です。
・その他記載されている会社名、製品名など名称は各社の登録商標または商標です。
コラム「製造業DX×3D成功のヒント」これまでの記事はこちらから
著者プロフィール
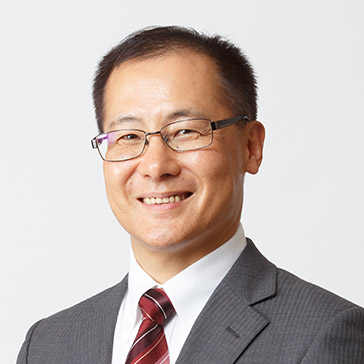
鳥谷 浩志(Hiroshi Toriya)
ラティス・テクノロジー株式会社 代表取締役社長/理学博士。株式会社リコーで3Dの研究、事業化に携わった後、1998年にラティス・テクノロジーの代表取締役に就任。超軽量3D技術の「XVL」の開発指揮後、製造業のデジタルトランスフォーメーション(DX)を3Dで実現することに奔走する。XVLは東京都ベンチャー大賞優秀賞、日経優秀製品サービス賞など、受賞多数。内閣府研究開発型ベンチャープロジェクトチーム委員、経済産業省産業構造審議会新成長政策部会、東京都中小企業振興対策審議会委員などを歴任。著書に 「製造業の3Dテクノロジー活用戦略」 「3次元ものづくり革新」 「3Dデジタル現場力」 「3Dデジタルドキュメント革新」 「製造業のDXを3Dで実現する~3Dデジタルツインが拓く未来~」などがある。
\お知らせ/ 「製造業のDXを3Dで実現する~3Dデジタルツインが拓く未来~」(幻冬舎)好評発売中。Amazon から購入いただけます。
最新のXVL関連情報をお届けするXVLメルマガを配信しています!